汽车电子系统正快速转变中,更多的电子元件与资讯应用被整合至汽车内,尤其是先进驾驶辅助系统(ADAS)、自驾车的图资与车联网,以及人工智慧(AI)应用的逐步落实,把越来越多的IC元件和电子模组带进汽车中,但也带来新的设计挑战,其中车用电路板(Printed-Circuit Board;PCB)、电路板组装(PCB Assembly; PCBA)与其板阶可靠度(Board Level Reliability;BLR)的验证更是关键的一环。
在车用电路板(PCB)方面,国际电子工业联接协会(IPC)已在2016年颁布了汽车专用的PCB验证及允收规范IPC-6012DA,其中包含了温度冲击耐久试验、高温耐久试验、高温高湿储存试验、阳极细丝导通试验(CAF)、表面绝缘电阻试验(SIR)等,这些测试当大量电子零组件导入汽车时,更成为国际汽车电子制造业者必须更关注的项目。
而在车用电路板组装(PCBA)上,由于顾及环保需求,无铅制程也开始导入在车电零组件设计中;AEC在2009年发布了Q005,启动了无铅制程的转换,接着在2014年的AEC Q100改版作业中,加入了无铅测试的要求,包含焊锡性测试、焊锡耐热试验及锡须试验,开启了汽车电子无铅制程的验证。
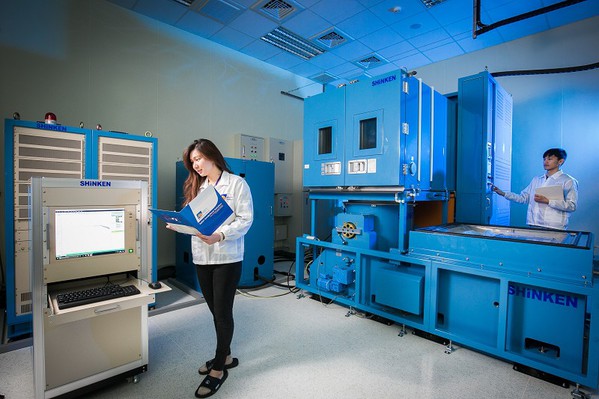
图一 : 宜特专为汽车电子验证建置的复合式振动测试实验室 |
|
至于板阶可靠度(BLR),则是国际间常用来验证IC元件上板至PCB之焊点强度的测试方式,是目前手持式装置常规的测试项目。而随着汽车电子系统的复杂度提升,更多的IC元件被运用在汽车内,BLR遂逐步成为车电重要测试项目之一,不仅Tier 1车厂BOSCH、Continental、TRW对此制定专属验证手法,令人注意的是AEC汽车电子协会最新出炉的AEC-Q104,明确定义了车用电子的板阶可靠性实验(Board Level Reliability)项目,虽然项目仅三项(TCT温度循环 / Drop落下 /Start up &Temperature Steps, STEP)尚未能完全贴近Tier 1的客户规范,但却是车用板阶可靠性通用标准发展的一大步。
宜特与德凯宜特提供一条龙服务 消除车电可靠度疑虑
电子产品验证服务商宜特科技(iST),与其转投资之关联企业德凯宜特(DEKRA iST)两者能提供全球最完整的汽车电子验证服务,从IC元件到系统端一条龙的完整验证项目。其中宜特在IC与BLR的验证上已有超过十年的经验,可针对车用IC与BLR项目进行验证;德凯宜特则能提供车用电路板(PCB)、电路板组装(PCBA)、车灯(LED)与系统模组的验证服务,两者能协助车电业者一次解决车用IC、PCB与PCBA、BLR、系统模组的验证问题。
宜特表示,为了实践智慧车的应用,汽车制造商必须在车体内放入更多的电子系统,也会使用更多的IC;另一方面,为了在车体内容纳更多IC,车用IC的封装也转为尺寸更小的先进3D堆叠封装技术,然而此技术使得焊点的间距更小、IC尺寸厚度增加,导致元件焊点须承受更大的应力,因此IC元件上板至PCB的焊点可靠度验证,也就是所谓的板阶可靠度(BLR),将是车电业者需要考量的新课题。
宜特指出,焊点崩裂(chipping)和破裂(crack)是造成元件失效的主因,这也是目前车电业者须进行BLR验证的关键。由于车用环境存在更强烈且严荷的挑战(包含各种路况的震动或汽车引擎运转所产生的温度变化),再加上汽车使用年限也非常长,动辄达到十年以上,因此非常考验汽车元件焊点的耐用度。
为了更贴近实际的车用环境,提高验证的准确度,宜特进一步表示,BLR验证包含应力与环境测试两部分,其测试项目包括温度循环、温度冲击、应力冲击与焊点接合强度测试(推力、拉力、弯曲),其中最关键的测试项目:温湿度复合式振动,将可模拟车辆的实际环境,测试IC元件上板至PCB后,在真实的温湿度与振动应力环境下的可靠性,借以协助业者达到车用的水准。
此外,在测试过程中使用Daisy Chain的设计,能即时监控样品的良率,且能准确撷取失效的时间点,让客户能更深入了解其产品的弱点,并及早进行改善。
而在汽车PCB与PCBA的验证部分,德凯宜特指出,一般电子元件若故障,可透过重工(Re-work)进行元件的更换,但若PCB故障,不可能移除所有元件后再更换PCB,因此PCB的品质是汽车电子系统中非常关键的一环,其耐用度更是车电业者所不能轻忽的项目。而PCBA是元件上板之后的半成品或次系统,是更接近实际系统环境的产品,针对PCBA进行验证,更能反映产品的真实可靠度。
由于长期与国际车厂及Tier 1供应商合作,宜特和德凯宜特非常熟悉汽车行业间的需求与规范,能带领车用供应商快速理解相关的规范,协助客户厘清其产品所需的验证项目,并能依据客户的需求提供客制化、循序渐进的服务,助其以阶段式的方式逐步落实各个验证项目,发挥最佳的经济效益。